|
行业标准(0)
- 全部 AQ 安全生产( 0 ) BB 包装( 0 ) CB 船舶( 0 ) CH 测绘( 0 ) CJ 城镇建设( 0 ) CM 国密( 0 ) CY 新闻出版( 0 ) DA 档案( 0 ) DB 地震( 0 ) DL 电力( 0 ) DZ 地质矿产( 0 ) EJ 核工业( 0 ) FZ 纺织( 0 ) GA 公共安全( 0 ) GBZ 职业卫生( 0 ) GC 物资储备( 0 ) GH 供销( 0 ) GM 密码( 0 ) GY 广播电影电视( 0 ) HB 航空( 0 ) HG 化工( 0 ) HJ 环境保护( 0 ) HS 海关( 0 ) HY 海洋( 0 ) JB 机械( 0 ) JC 建材( 0 ) JG 建筑工业( 0 ) JR 金融( 0 ) JS 机关事务行业标准( 0 ) JT 交通( 0 ) JY 教育( 0 ) LB 旅游( 0 ) LD 劳动和劳动安全( 0 ) LS 粮食( 0 ) LY 林业( 0 ) MH 民用航空( 0 ) MR 市场监管行业标准( 0 ) MT 煤炭( 0 ) MZ 民政( 0 ) NB 能源( 0 ) NY 农业( 0 ) QB 轻工( 0 ) QC 汽车( 0 ) QJ 航天( 0 ) QTE 行业标准英文版( 0 ) QX 气象( 0 ) RB 认证认可标准( 0 ) SB 商业( 0 ) SC 水产( 0 ) SF 司法( 0 ) SH 石油化工( 0 ) SJ 电子( 0 ) SL 水利( 0 ) SN 商检( 0 ) SW 税务( 0 ) SY 石油天然气( 0 ) TB 铁路运输( 0 ) TD 土地管理( 0 ) TY 体育( 0 ) WB 物资管理( 0 ) WH 文化( 0 ) WJ 兵工民品( 0 ) WM 外经贸( 0 ) WS 卫生( 0 ) WW 文物( 0 ) XB 稀土( 0 ) XF 消防( 0 ) YB 黑色冶金( 0 ) YC 烟草( 0 ) YD 通信( 0 ) YS 有色冶金( 0 ) YY 医药( 0 ) YZ 邮政( 0 ) ZY 中医药( 0 )
国际标准 (0)
- 全部 01 综合、术语学、标准化、文献( 0 ) 03 社会学、服务、公司(企业)的组织和管理、行政、运输( 0 ) 07 自然和应用科学( 0 ) 11 医药卫生技术( 0 ) 13 环保、保健和安全( 0 ) 17 计量学和测量、物理现象( 0 ) 19 试验[该类仅包括试验通用标准;分析化学,见71.040]( 0 ) 21 机械系统和通用件( 0 ) 23 流体系统和通用件[流体流量的测量,见17.120]( 0 ) 25 机械制造[该类包括通用标准]( 0 ) 27 能源和热传导工程( 0 ) 29 电气工程( 0 ) 31 电子学( 0 ) 33 电信、音频和视频工程( 0 ) 35 信息技术( 0 ) 37 成像技术( 0 ) 39 精密机械、珠宝( 0 ) 43 道路车辆工程( 0 ) 45 铁路工程( 0 ) 47 造船和海上构筑物( 0 ) 49 航空器和航天器工程( 0 ) 53 材料储运设备( 0 ) 55 货物的包装和调运( 0 ) 59 纺织和皮革技术( 0 ) 61 服装工业( 0 ) 65 农业( 0 ) 67 食品技术( 0 ) 71 化工技术( 0 ) 73 采矿和矿产品( 0 ) 75 石油天然气及相关技术( 0 ) 77 冶金( 0 ) 79 木材技术( 0 ) 81 玻璃和陶瓷工业( 0 ) 83 橡胶和塑料工业[其他高分子材料入此]( 0 ) 85 造纸技术( 0 ) 87 涂料和颜料工业( 0 ) 91 建筑材料和建筑物( 0 ) 93 土木工程( 0 ) 95 军事物资、军事工程、武器( 0 ) 97 家用和商用设备、文娱、体育( 0 ) 99 (无标题)[该类保留出,作为内部其他用途]( 0 )
国外标准 (0)
- 全部 ANSI 美国国家标准学会( 0 ) API 美国石油学会( 0 ) AS 澳大利亚标准( 0 ) ASME 美国机械工程协会( 0 ) ASTM 美国材料与试验协会标准( 0 ) BS 英国标准( 0 ) BSI 英国BSI标准( 0 ) CFR 美国联邦法规( 0 ) CSA 加拿大标准( 0 ) DE 德国标准( 0 ) DIN 德国DIN标准( 0 ) EN 欧洲标准( 0 ) FR 法国标准( 0 ) IEEE 美国电气电子工程师协会( 0 ) JP 日本标准( 0 ) JSA 日本JIS标准( 0 ) KS 韩国标准( 0 ) MIL 美国军用标准( 0 ) SAE 美国机动车工程师学会( 0 ) SU 俄罗斯GOST标准( 0 ) UL 美国保险商试验室( 0 ) UNI 意大利标准( 0 )
地方标准(0)
- 全部 DB11 北京市地方标准( 0 ) DB12 天津市地方标准( 0 ) DB13 河北省地方标准( 0 ) DB14 山西省地方标准( 0 ) DB15 内蒙古自治区地方标准( 0 ) DB21 辽宁省地方标准( 0 ) DB22 吉林省地方标准( 0 ) DB23 黑龙江省地方标准( 0 ) DB31 上海市地方标准( 0 ) DB32 江苏省地方标准( 0 ) DB33 浙江省地方标准( 0 ) DB34 安徽省地方标准( 0 ) DB35 福建省地方标准( 0 ) DB36 江西省地方标准( 0 ) DB37 山东省地方标准( 0 ) DB41 河南省地方标准( 0 ) DB42 湖北省地方标准( 0 ) DB43 湖南省地方标准( 0 ) DB44 广东省地方标准( 0 ) DB45 广西壮族自治区地方标准( 0 ) DB46 海南省地方标准( 0 ) DB50 重庆市地方标准( 0 ) DB51 四川省地方标准( 0 ) DB52 贵州省地方标准( 0 ) DB53 云南省地方标准( 0 ) DB54 西藏自治区地方标准( 0 ) DB61 陕西省地方标准( 0 ) DB62 甘肃省地方标准( 0 ) DB63 青海省地方标准( 0 ) DB64 宁夏回族自治区地方标准( 0 ) DB65 新疆维吾尔自治区地方标准( 0 )
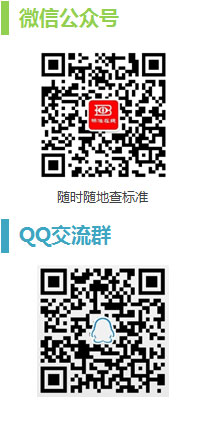
QQ交流1群(已满)
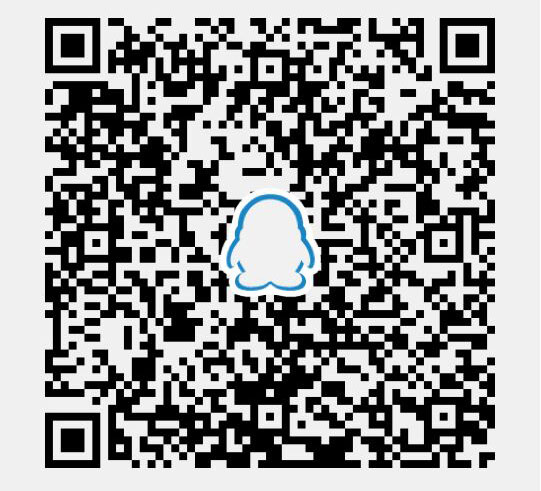
QQ交流2群